PLASTIC INJECTION MOULDING
Lunar Enterprise utilizes a rapid injection moulding technology where CAD models are sent to the shop floor for mould milling. Depending of the life-cycle of the product, moulds are made, ranging from heavy duty to simple ones. Ideas can be transformed into design in as fast as 1 month. We also offer secondary services to support your project, so that you don't have to go through different suppliers to get your final product made. We have our own machine shop, which allows to reduce delays due to breakdown and delay from other suppliers.
Why choose Lunar Enterprise?
We have more than 45 years of experience in Injection Moulding. When you visit our workshop, you can find retro-grade injection moulding machines as well as hi-tech injection moulding machines which are industry-4.0 ready and robot-enabled.
We also offer secondary services to fulfill the entire manufacturing needs at one place.
What is Injection Moulding?
Injection molding, the most popular process for manufacturing thermoplastic products, consists of injecting molten plastic material from a heated cylinder into a closed mold, allowing the plastic to cool down and solidify, and ejecting the finished product from the mold. The machine consists of an injection unit to inject the material, and a clamping unit that is used to hold the mold closed during the injection phase.
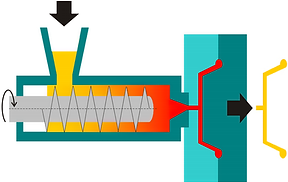

What is High Speed Injection Moulding?
There are many stages in an injection molding process which contributes to big chunk of cycle time. However, optimizing the stages in such a way to get the least cycle time, while maintaining the product defect-free is what happens in High Speed Injection Moulding.
Cost effectiveness in Injection Moulding
There are two things that affects the cost of an injection molded product. First comes the mold complexity and then the type of raw material used.
How to reduce mould costs?
-
Eliminate undercuts
-
Use a core cavity approach
-
Get rid of unnecessary features
-
Reduce cosmetic finishes and approaches
-
Use multi-cavity mold